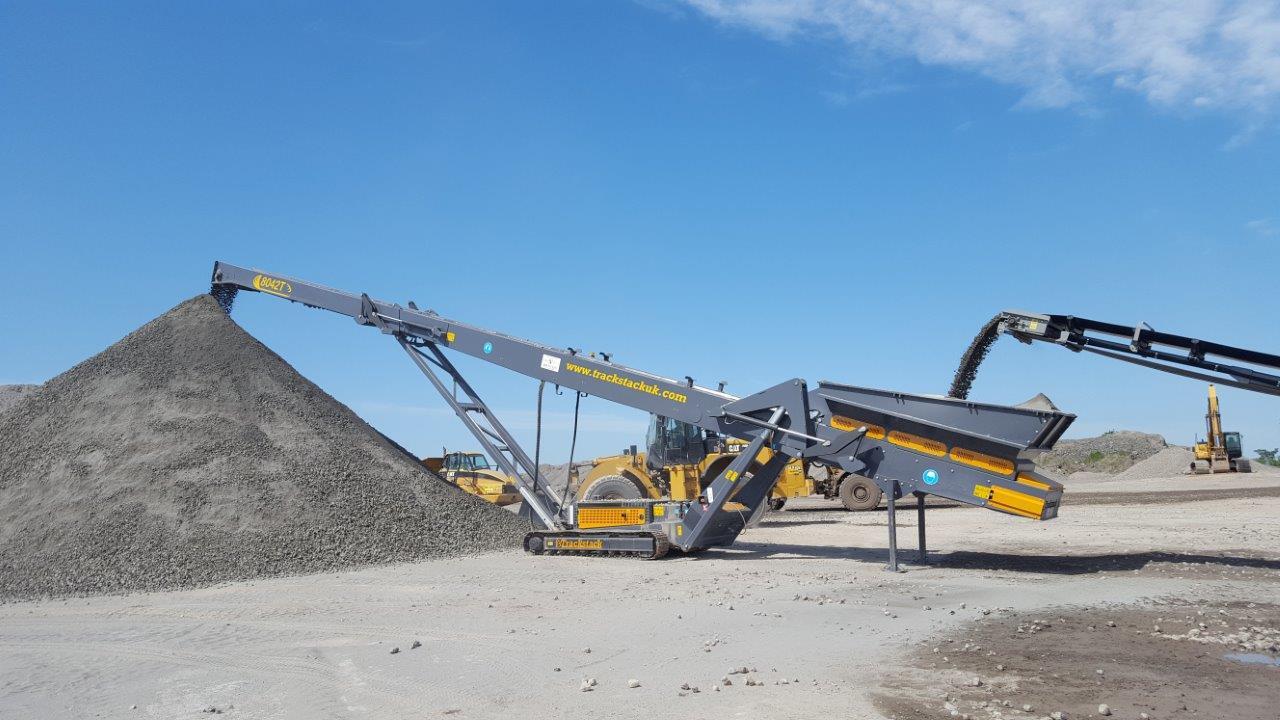
Stack Smart: How to Select the Right Stacker for Efficient Material Handling
In the material handling industry, efficiency and precision are key to maximising productivity, and stackers play a vital role in achieving that. Whether you’re stockpiling or organising raw materials, stackers are indispensable for creating high capacity storage solutions. These machines, manufactured for heavy-duty tasks, ensure that materials are stored safely and systematically while reducing labor and operational costs.
This blog will delve into the Tesab, Lippmann, and McCloskey Environmental stackers available at Stewart Plant Sales, and how to choose the right one for your needs.
What is a Stacker?
A stacker is a type of bulk material handling equipment used to efficiently move, lift, and stack large amounts of material such as coal and gravel. These machines are commonly used in industries like mining, quarrying, construction, and waste management where high capacity storage and precise material handling are essential.
Typically mounted on tracks, rails, or wheels, stackers transport materials via their conveyor system and deposit them in organised, uniform piles or stockpiles. They have fixed or adjustable booms, which allow them to evenly distribute materials over a wide area.
Stackers improve operational efficiency by automating the stacking process, reducing labour costs and optimising storage space. In many operations, they are placed in a train after a reclaimer, which retrieves the stacked material when needed.
How Do Stackers Work?
The process of material handling using a stacker normally involves several key steps, ensuring efficient movement, stacking, and storage of bulk materials.
- Loading Material: Material is loaded onto a feed conveyor or directly into the stackers hopper.
- Stacking Material: Once at the desired location, the stacker’s boom is positioned to deposit the material. The operator can adjust the height and angle of the boom to control the stacking process.
- Creating Stockpiles: The stacker builds the stockpile layer by layer, ensuring uniformity and stability in the piles. The operator can monitor the process the achieve the desired shape and height.
- Completion and Monitoring: Once the stockpile is complete, the stacker may make final adjustments to ensure that the material is evenly distributed.
The Key Components of a Stacker
These components work together to ensure that stackers operate efficiently and effectively in handling and storing bulk materials.
- Boom: The extendable arm that supports the conveyor system and can be raised, lowered, and in some cases rotated to reach various stacking heights and angles.
- Conveyor system: A belt or series of belts that transport materials from the loading area to the discharge point on the boom.
- Material Hopper: The container at the loading end of the stacker where bulk materials are inserted to be organised.
- Undercarriage: This is the supporting structure that includes wheels or tracks for mobility, ensuring stability and ease of movement across the stacking area.
Key Benefits of Stackers
Efficiency
Increased Throughput
Stackers automate the process of moving and stacking bulk materials. This significantly speeds up operations compared to manual handling, leading to higher productivity and more efficient use of time.
Space Optimisation
Stackers are manufactured to produce organised and stable stockpiles, allowing for better use of available storage space. By creating uniform piles, wasted space is minimised which further improves accessibility to materials when needed.
Improved Workflow
Introducing stackers to your reclaimers and other material handling machines, streamlines the overall workflow. This allows for continuous cycle of loading, stacking, and reclaiming, enhancing operational efficiency.
Safety
Enhanced Stability
Stackers reduce the risk of stockpiled materials from collapsing or spilling, enhancing safety for working in the vicinity of the stacking area.
Improved Visability
Many stackers are designed with operators in mind, and so feature clear sightlines to monitor operations, helping them maintain awareness of their surroundings, further reducing the risk of accidents.
Choosing the Right Stacker for Your Needs
Load Capacity
The most important factor to consider when choosing the right stacker is the load capacity. You must make sure the stacker can handle the maximum weight of the goods you will be moving. You should also consider the type of material you are handling, and their weight.
Size of Loads
In addition to weight, load size should play an important role when you’re choosing the right stacker. Large or oddly shaped loads may require a stacker with adjustable forks or more flexible handling capabilities.
Lifting Height
It is important to assess the height to which you need to lift your loads, different stackers are designed for various height ranges, and so choose a model that can meet your stacking needs.
Brand Reputation
It is important to choose stackers from a reliable manufacturer with a strong reputation for quality and customer service. That’s why at Stewart Plant Sales, we offer stackers from manufactures Tesab, Lippmann, and McCloskey Environmental.
Tesab Stackers
Stewart Plant Sales offers different Tesab stackers with varied capacities. These machines are renowned for being robust and reliable, designed for many applications.
Tesab Trackstack 6536T
This stacker is compact but powerful featuring Tesab’s innovative Trackstack boomerang design. This enables the feed boom height to be adjusted without altering the position of the head drum.
- Stockpile Height: 8.36m
- Weight: 14,000kg
- Engine: CAT2.2
- Download Brochure
Tesab 5040SF Feeding Stack
The Tesab 5040SF feeding stack model is equipped with a 10ft feeder hopper that transfers material onto a 50ft conveyor. This system eliminates the need for double handling of materials.
- Hopper Capacity: 6m3
- Engine: 74Hp
- Weight; 145,000kg
- Download Brochure
Tesab 8048SF Feeding Stack
This model of stacker is fairly similar to the Tesab 5040SF Feeding Stack however, the 8048SF is equipped with a much larger feeder and conveyor to handle those more demanding operations.
- Hopper Capacity: 13m3
- Engine: 127Hp
- Weight: 245,000kg
- Download Brochure
View the full Tesab Stacker range from Stewart plant Sales.
Lippmann Stackers
Stewart Plant Sales also offer a range of Lippmann stackers, designed to meet high standards of productivity and efficiency.
Lippmann 4065ST
This model is highly mobile and productive, allowing for operators to stockpile/transfer material directly from mobile crushing and screening plants.
- Hopper Volume: 1.1m3
- Weight: 10,500kg
- Engine: 36.5kW
- Download Brochure
Lippmann 4080ST
This model’s versatility is demonstrated across a wide application base, delivering a stockpiling process that is as fast.
- Stockpile Height: 8.89m
- Weight: 12,700kg
- Engine: 49Hp
- Download Brochure
Lippmann 80SF
The Lippmann 80sf is the latest stacker offered by Lippmann. It comprises of a large feeder hopper that transfers material onto a 80ft conveyor.
- Stockpile Height: 8.89m
- Weight: 12,700kg
- Engine: CAT2.2
- Download Brochure
View the full Lippmann Stacker range from Stewart Plant Sales.
McCloskey Environmental Stackers
Available from Stewart Plant Sales, are a vast variety of McCloskey Environmental Stackers that are designed to help minimise the world’s waste.
McCloskey Environmental EC-50
This machine is a light-duty, highly mobile wheeled stacker, manufactured for both stockpiling and material transfer
- Stockpile Height: 6.365m
- Weight: 4,100kg
- Engine: 49Hp
- Download Brochure
McCloskey Environmental EC-65T
This McCloskey model is built for high capacity stockpiling. The EC-65T is manufactured with an impressive variety of features, including a large hopper and full length guarding.
- Stockpile Height: 7.88m
- Weight: 10,500kg
- Engine: Diesel/Dual Power
- Download Brochure
McCloskey Environmental EC-80T
The ET-80T is designed to allow operators to stockpile/transfer material directly from shredding and recycling plants.
- Stockpile Height: 8.898m
- Weight: 12,700kg
- Engine: Diesel/Dual Power
- Download Brochure
View all the McCloskey Environmental stackers available at Stewart Plant Sales
If you would like any further information or would like to enquire about one of the stackers available at Stewart Plant Sales, please contact us here.